Radiator recore
-
- 1275 Cooper S
- Posts: 2354
- Joined: Fri Jun 25, 2010 10:57 am
- Location: Colchester, Essex
- Has thanked: 7 times
- Been thanked: 6 times
Radiator recore
Folks, How tricky would it be to recore a radiator? I have several Coventry Radiators for my different cars and have used the Minispares two core successfully. What kind of job is it to fuse the core from the two core onto the headers from a Coventry rad? Is it beyond DIY scope? Cheers
Rolesyboy
-
- Basic 850
- Posts: 65
- Joined: Thu Jun 24, 2010 2:23 pm
Re: Radiator recore
Hi , i just had a call with someone who does it fot his job ; restauring radiators.
He can put the old header and underside on your ,or his, new core.
The job is pretty easy if you have the knowledge.
I would not recommend doing it yourself,it is going to get very messy.
There should be company's in your country too ,it's an old steel ,but still needed.
In the netherlands it cost around 120 euro with a new core.You can get different core's for abround the same money.
He can put the old header and underside on your ,or his, new core.
The job is pretty easy if you have the knowledge.
I would not recommend doing it yourself,it is going to get very messy.
There should be company's in your country too ,it's an old steel ,but still needed.
In the netherlands it cost around 120 euro with a new core.You can get different core's for abround the same money.
- Spider
- 1275 Cooper S
- Posts: 4805
- Joined: Mon May 07, 2012 6:10 am
- Location: Big Red, Australia
- Has thanked: 125 times
- Been thanked: 34 times
Re: Radiator recore
Definitely possible at home. The odd ball and special radiators I have been doing myself for over 30 years now, you don't need much more than a gas blow torch, however you do want about a 30 - 35 mm dia nozzle for it, not that you need (or want!) a hot flame, but a broad flame. You'll also want a means of holding the radiator, I current use a 'workmate'. one of the small fold up benches for builders, that has the long clamp up top
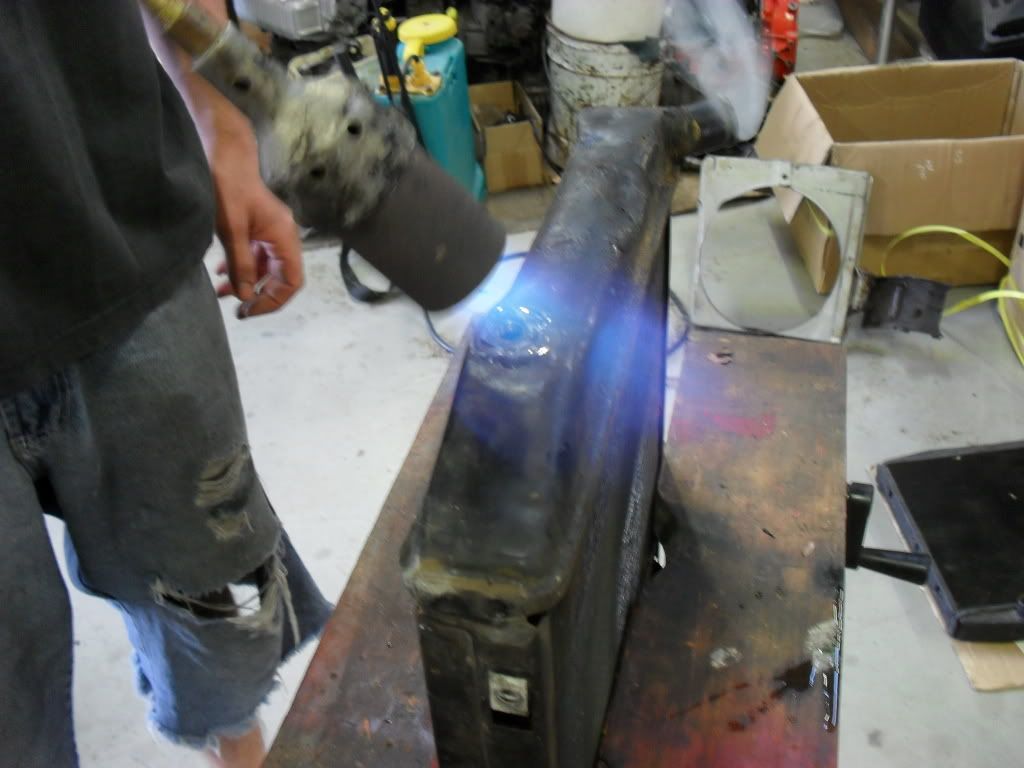
Some paste type fluxes, 3 - 4 mm solder, I prefer then non fluxed type and for some of the repairs, I also use Plumbing Metal, which is similar to solder, but more like plasticine, the old school body guys also use this as body filler.
The metal sides are soldered and riveted on to the header tanks. I usually find it best to linish the heads of those rivets off rather than trying to drill them to get it apart. After linishing, just warm them a bit to melt the solder. They are riveted as solder alone is not nearly strong enough, especially with vibration, to hold them together. Look around for some copper or monel pop rivets to use for re-assembly. Try the smaller ship chandlers or plumber's suppliers as they usually have them in small packs of 10 or so as they are dear and it's unlikely you'll go through a box of 1000!
Don't get the parts any hotter than needed for the solder operations,
Have some practice goes at soldering. This type of soldering, while the same in principal to doing say wires, is vastly different in practice!
Be sure everything is really clean before trying to re-solder. I start off wire wheeling them, then use steel wool. For the really grubby stuff, I put them in the acid to clean them up.
I made up a plugs for pressure testing from some heater hose, a bolt, washers and a nut
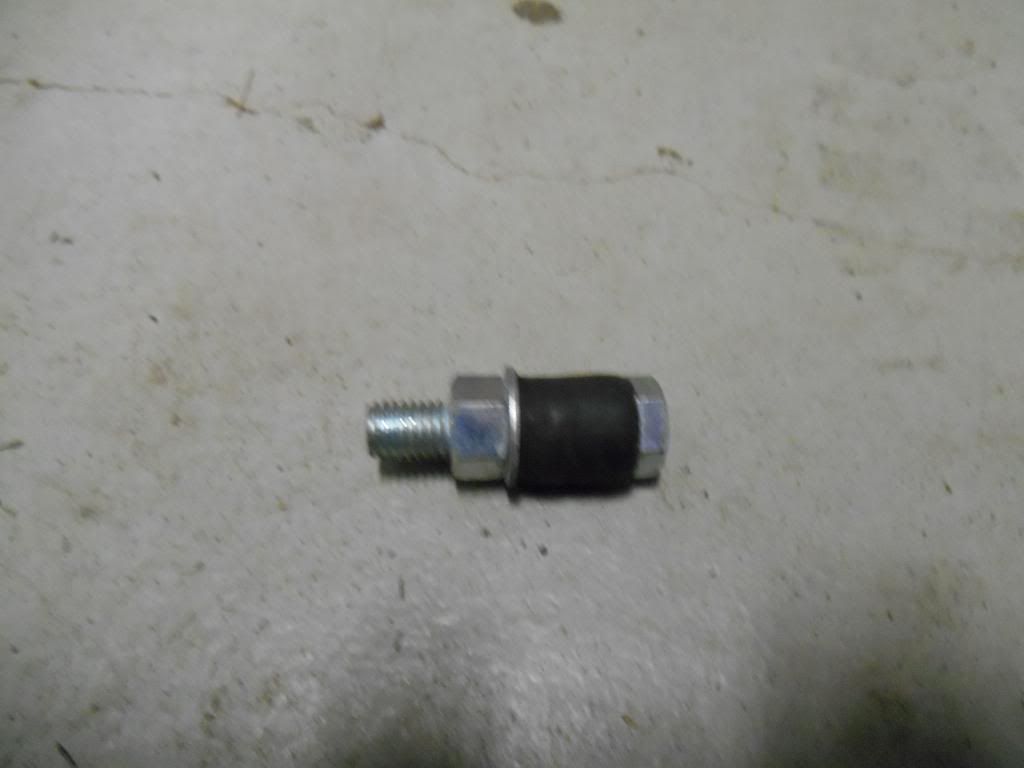
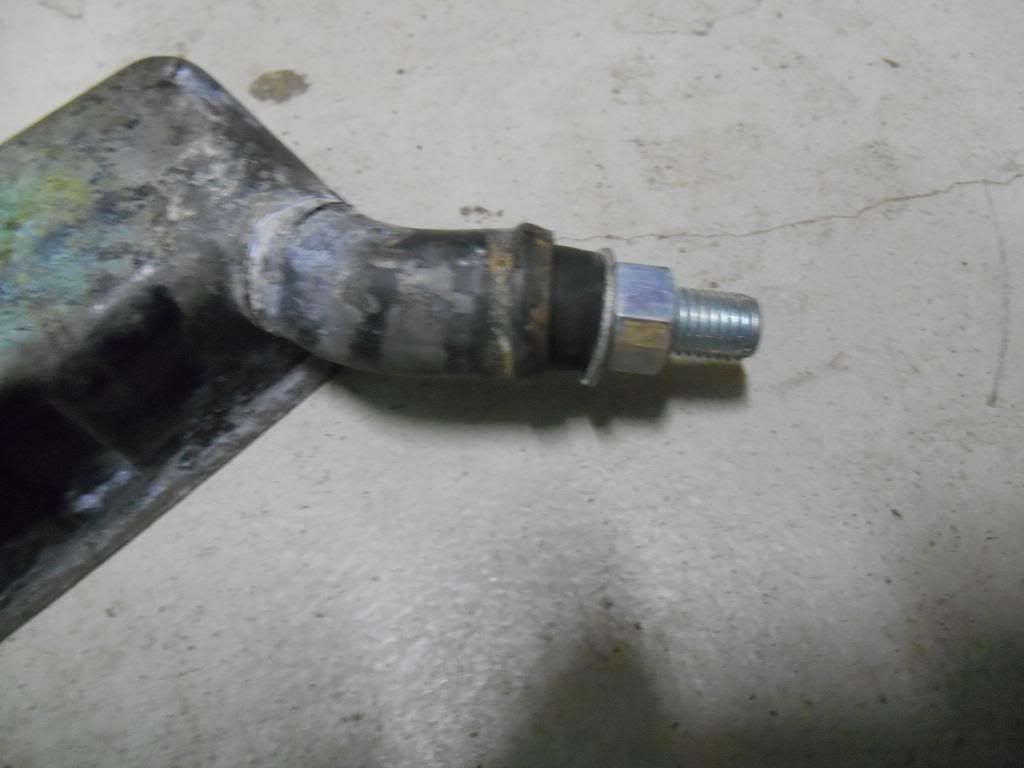
Or there are commercial types available, but I find the home brewed ones better
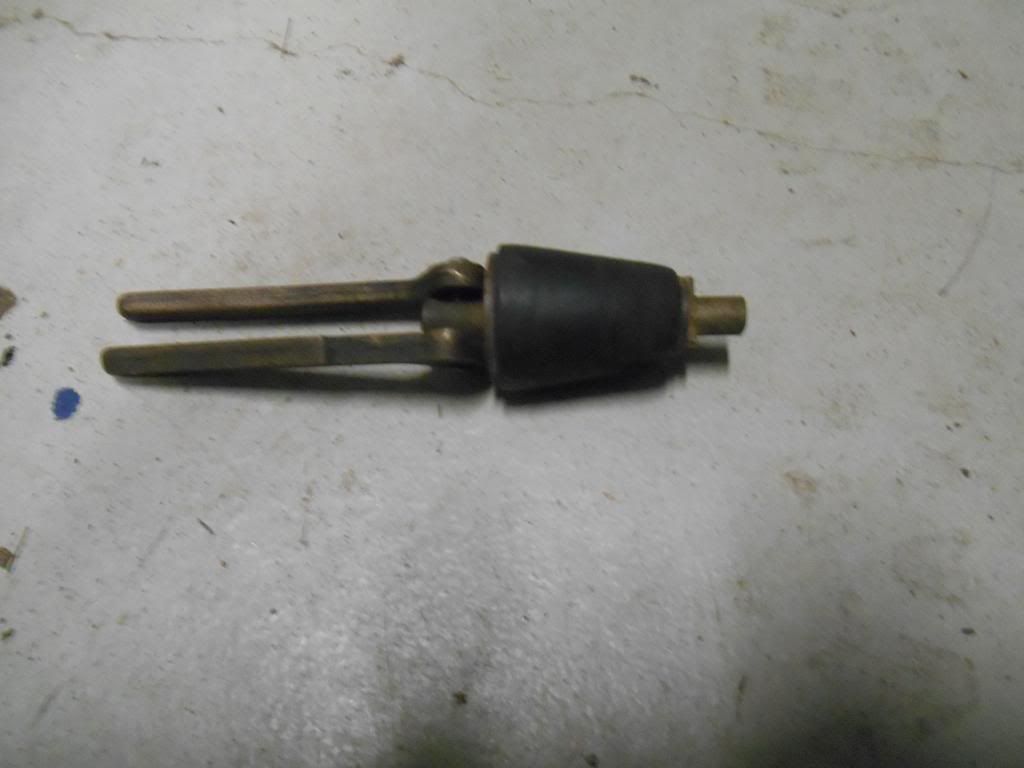
Fit a blanking ca[ and then use a hand tyre pump on the over-flow outlet to pressurise it to check for leaks, though these days, I I have a commercial type tester / pump.
Don't expect your first to be a success, however, it will be rewarding
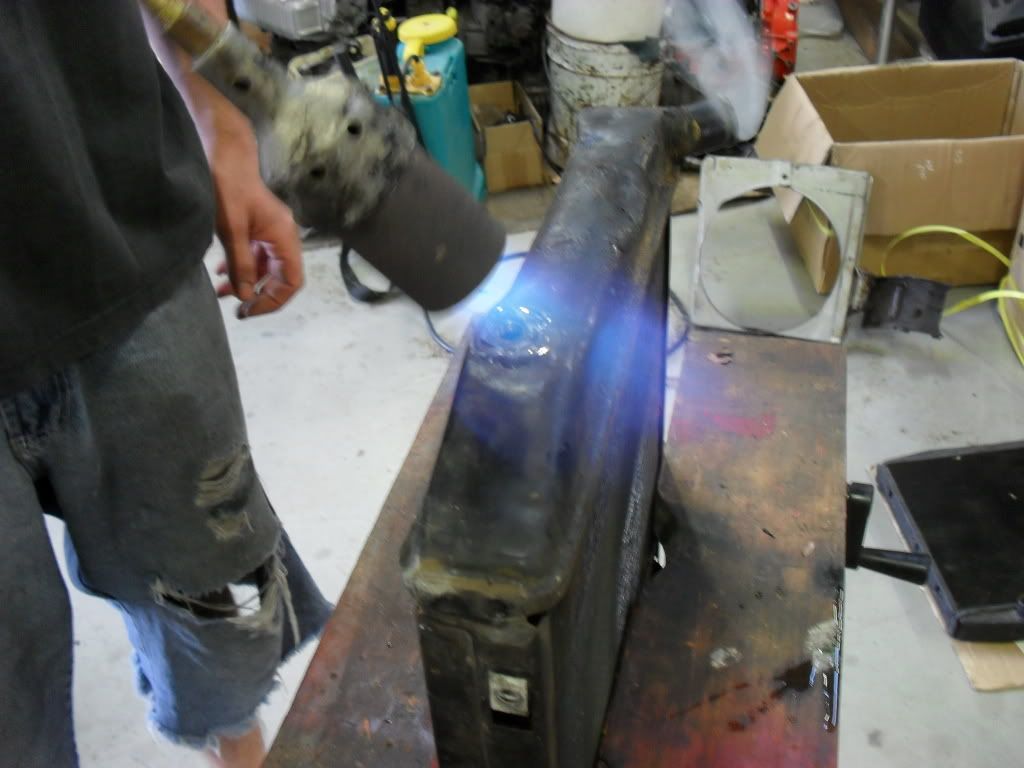
Some paste type fluxes, 3 - 4 mm solder, I prefer then non fluxed type and for some of the repairs, I also use Plumbing Metal, which is similar to solder, but more like plasticine, the old school body guys also use this as body filler.
The metal sides are soldered and riveted on to the header tanks. I usually find it best to linish the heads of those rivets off rather than trying to drill them to get it apart. After linishing, just warm them a bit to melt the solder. They are riveted as solder alone is not nearly strong enough, especially with vibration, to hold them together. Look around for some copper or monel pop rivets to use for re-assembly. Try the smaller ship chandlers or plumber's suppliers as they usually have them in small packs of 10 or so as they are dear and it's unlikely you'll go through a box of 1000!
Don't get the parts any hotter than needed for the solder operations,
Have some practice goes at soldering. This type of soldering, while the same in principal to doing say wires, is vastly different in practice!
Be sure everything is really clean before trying to re-solder. I start off wire wheeling them, then use steel wool. For the really grubby stuff, I put them in the acid to clean them up.
I made up a plugs for pressure testing from some heater hose, a bolt, washers and a nut
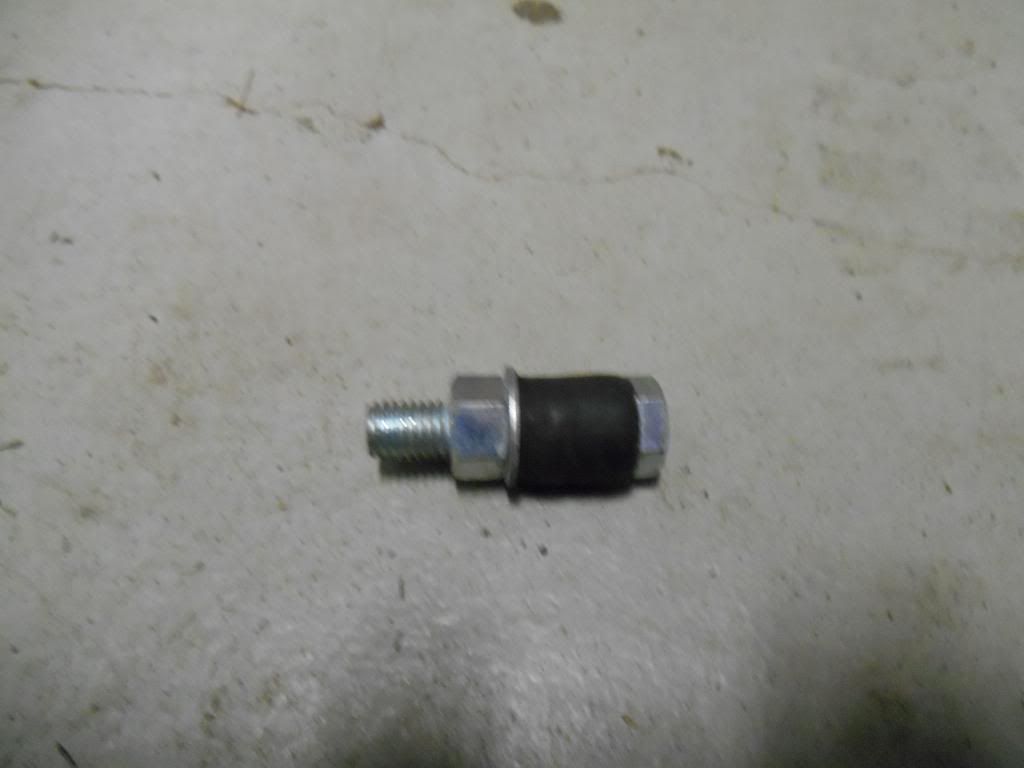
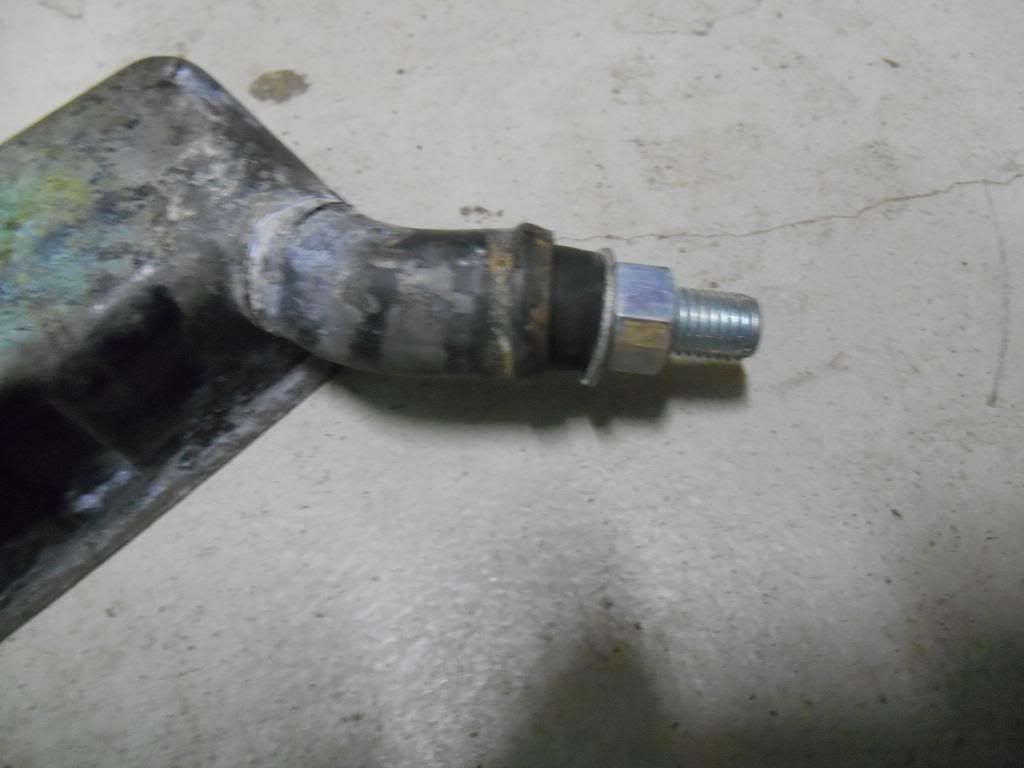
Or there are commercial types available, but I find the home brewed ones better
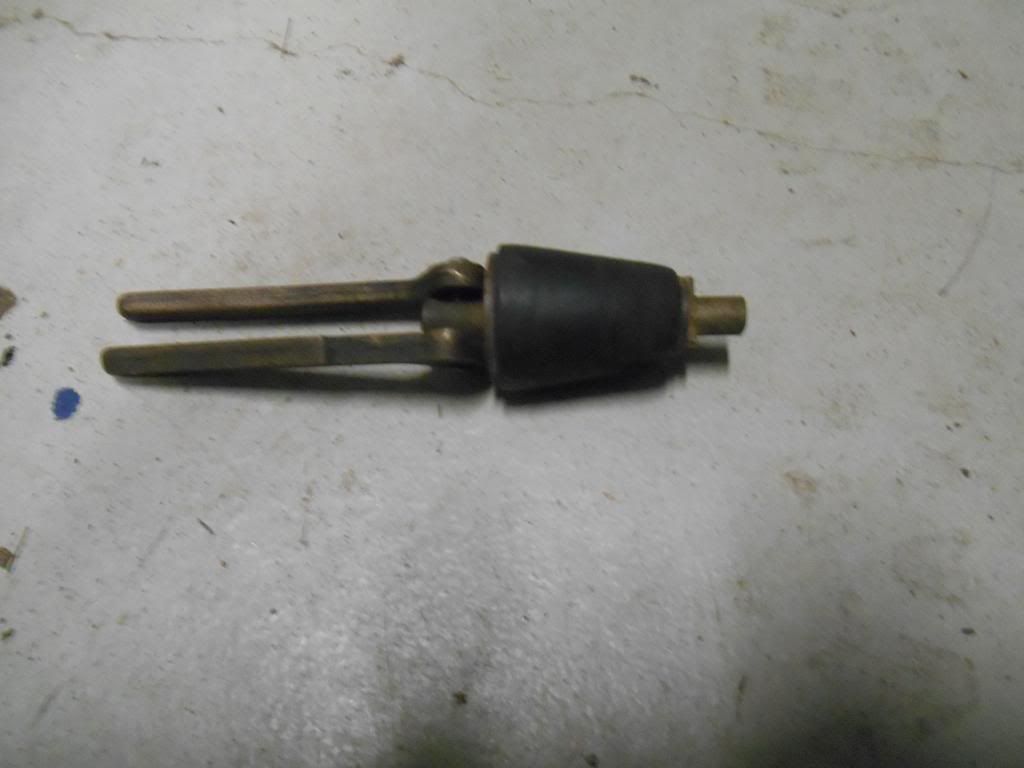
Fit a blanking ca[ and then use a hand tyre pump on the over-flow outlet to pressurise it to check for leaks, though these days, I I have a commercial type tester / pump.
Don't expect your first to be a success, however, it will be rewarding

Re: Radiator recore
Plumbing solder and body solder aren't the same thing, body solder has more Tin in it.
- dklawson
- 1275 Cooper S
- Posts: 1166
- Joined: Tue Feb 18, 2014 4:44 am
- Location: Durham, NC USA
- Been thanked: 1 time
- Contact:
Re: Radiator recore
Spider, I am truly impressed !
I do virtually all my own car work but I have never even considered major radiator work.
I do virtually all my own car work but I have never even considered major radiator work.
Doug L.
-
- 1275 Cooper S
- Posts: 2354
- Joined: Fri Jun 25, 2010 10:57 am
- Location: Colchester, Essex
- Has thanked: 7 times
- Been thanked: 6 times
Re: Radiator recore
Thanks Spider. Your encyclopaedic knowledge of theses things never fails to amaze me. You have spurred me on to have a go. I will let know how it goes. Cheers . Mark
Rolesyboy
- Spider
- 1275 Cooper S
- Posts: 4805
- Joined: Mon May 07, 2012 6:10 am
- Location: Big Red, Australia
- Has thanked: 125 times
- Been thanked: 34 times
Re: Radiator recore
Shucks, thanks for the very kind comments guys,
but honestly, if it was hard, I couldn't do it
Rolesy, get an old radiator and have a practice with that.
Also, I should have mentioned that I solder all the parts on each header in one go. I've found that (for example) soldering the header tank, then fitting the inlet pipe then filler neck difficult at times and not the best way to go. Oh and with the particular fluxes I use, the one I use on the brass and copper parts (Solderine I think) doesn't work too good on steel (which the sides are), so I use a different flux for this, I think it's Bakers Soldering fluid. You may also find when starting off using a fluxed solder might be helpful, I just found it messy (at the end of the job) and I was going through a lot more of it.
Smiffy, Plumbing metal while appearing like solder is not solder. Solder (from memory) is around 35% lead / 65% tin while Plumbing Metal is 35% tin / 65% lead. When heated, solder will just be there one moment and on the floor the next, Plumbing Metal on the other hand has a high 'plastic' range (I think that's the term), so you can heat it, then push it around in to shapes and place it where you want it and as thick as you want it. Obviously it can't be done bare handed, for this I use a Mole Skin that's soaked in Tallow (very old school), I think the body guys use timber paddles dipped in wax, maybe someone else could confirm?
edit> this was one I did a few weeks back, I fitted 2mm steel sides to this one (as the stock ones always crack), the ends wrapping over the upper and lower tanks, then to give it some added strength (as well as improving the look of it) I filled them over with Plumping Metal
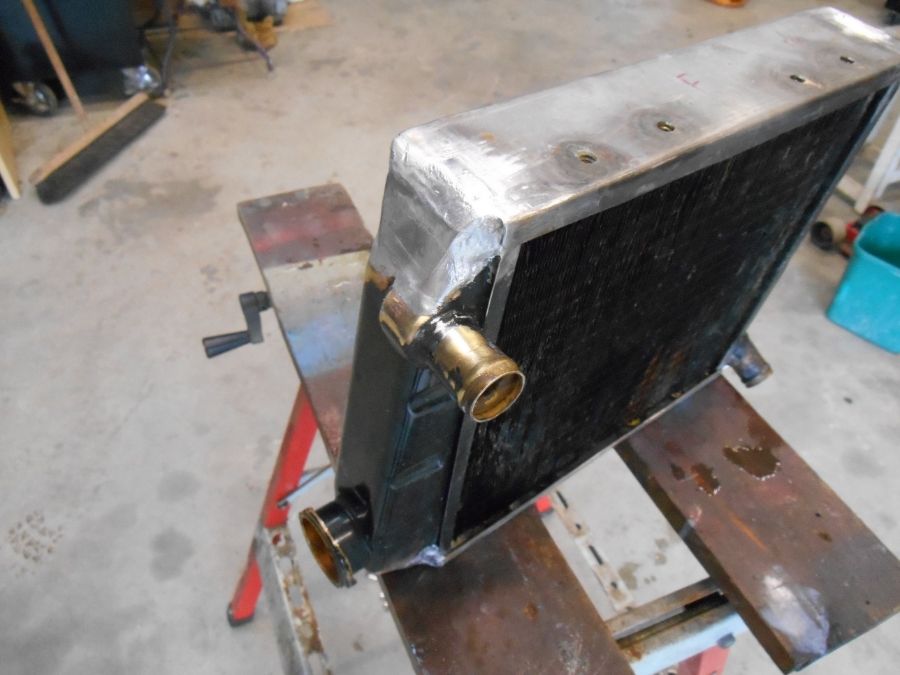


Rolesy, get an old radiator and have a practice with that.
Also, I should have mentioned that I solder all the parts on each header in one go. I've found that (for example) soldering the header tank, then fitting the inlet pipe then filler neck difficult at times and not the best way to go. Oh and with the particular fluxes I use, the one I use on the brass and copper parts (Solderine I think) doesn't work too good on steel (which the sides are), so I use a different flux for this, I think it's Bakers Soldering fluid. You may also find when starting off using a fluxed solder might be helpful, I just found it messy (at the end of the job) and I was going through a lot more of it.
Smiffy, Plumbing metal while appearing like solder is not solder. Solder (from memory) is around 35% lead / 65% tin while Plumbing Metal is 35% tin / 65% lead. When heated, solder will just be there one moment and on the floor the next, Plumbing Metal on the other hand has a high 'plastic' range (I think that's the term), so you can heat it, then push it around in to shapes and place it where you want it and as thick as you want it. Obviously it can't be done bare handed, for this I use a Mole Skin that's soaked in Tallow (very old school), I think the body guys use timber paddles dipped in wax, maybe someone else could confirm?
edit> this was one I did a few weeks back, I fitted 2mm steel sides to this one (as the stock ones always crack), the ends wrapping over the upper and lower tanks, then to give it some added strength (as well as improving the look of it) I filled them over with Plumping Metal
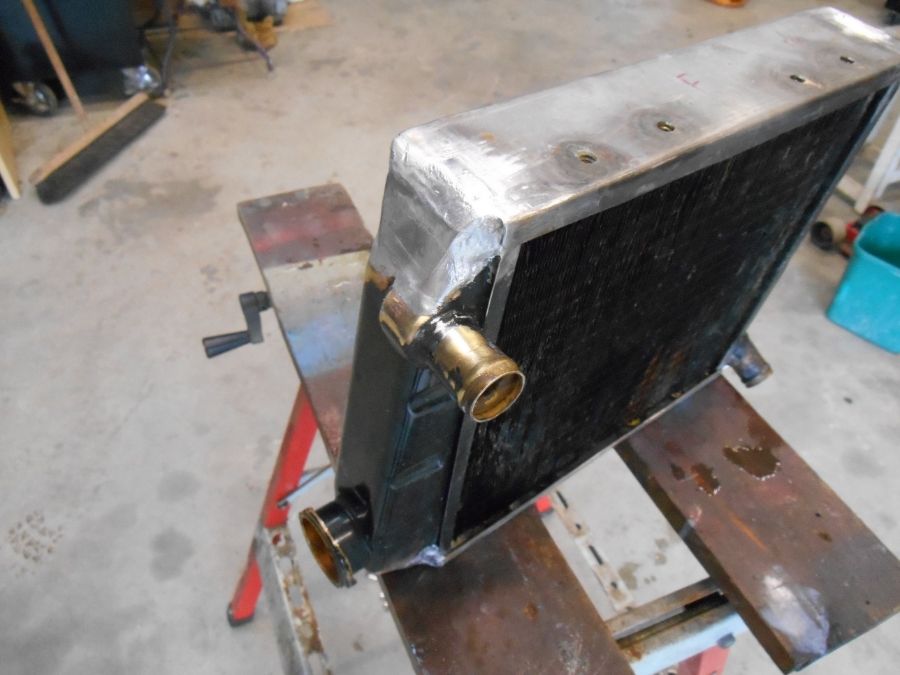
Re: Radiator recore
There is definitely an art to body soldering, but I find the opposite to be true.
You do not have the required permissions to view the files attached to this post.